Heat engines are the machine that converts the heat energy into the mechanical work. Based on the combustion process, these heat engines are classified as Internal combustion engines (ICE) and External combustion engines (ECE).
In this article, we will discuss Internal combustion engines in detail.
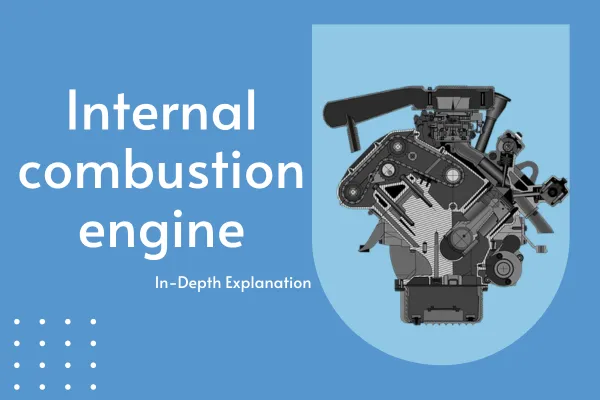
In this article, we’re going to discuss:
- What is an Internal combustion engine?
- Internal combustion engine history:
- Types of Internal combustion engines:
3.1. Type of gas flow:
3.2. Type of motion:
3.3. Number of strokes:
3.4. Ignition: - Major components of reciprocating IC engine:
- How does an Internal combustion (IC) engine work?
- Internal combustion engine efficiency:
- Uses of IC engines:
What is an Internal combustion engine?
Internal combustion (I.C.) engines are heat engines in which the combustion process is carried out internally, i.e., inside the combustion chamber. The high-pressure gases arise during the combustion are then used to do some useful work. This work is used to power the wide range of applications.
The below diagram tells us what is internal combustion engine and how it is different from external combustion engine.
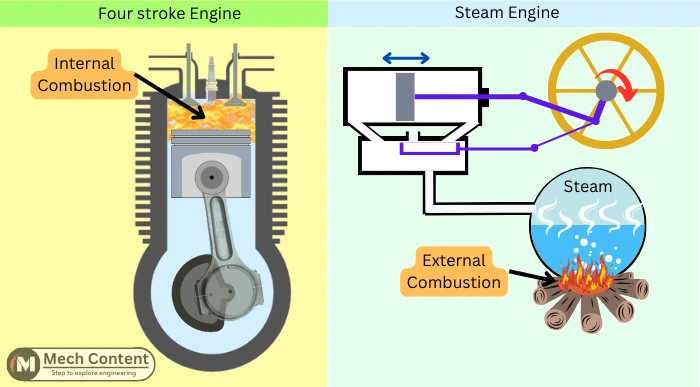
In IC engines, the combustion chamber is filled with a mixture of air and fuel (In some engines fuel is added later during combustion). This mixture is compressed to raise the temperature of the mixture. After that, this pressurized mixture is ignited to start the combustion process.
The combustion of the air-fuel mixture generates high-pressure gases that are further used for performing work.
In reciprocating engines (like above), the high-pressure gases pushes the piston while undergoing expansion. This movement of the piston is then converted into the crankshaft rotation.
In gas turbines, the high-pressure gases are expanded over the turbine blades to drive the turbine shaft. In jet engines, the high-pressure gases are directed using the nozzle to create a high thrust.
In IC engines, the combustion products (hot gases) act as a working fluid, Hence IC engine eliminates a lot of heat losses that occurs in external combustion engine. Thus these engines are considered more efficient than external combustion engines.
Internal combustion engine history:
From the middle of the 19th century, the internal combustion engine started to considerably evolve.
The first Petrol engine (SI) was built in 1876 by German engineer Nicolaus August Otto. The Diesel engine (CI) was invented in 1897 by German engineer Rudolf Diesel.
Here is a short overview of the Evolution history of the IC engine.
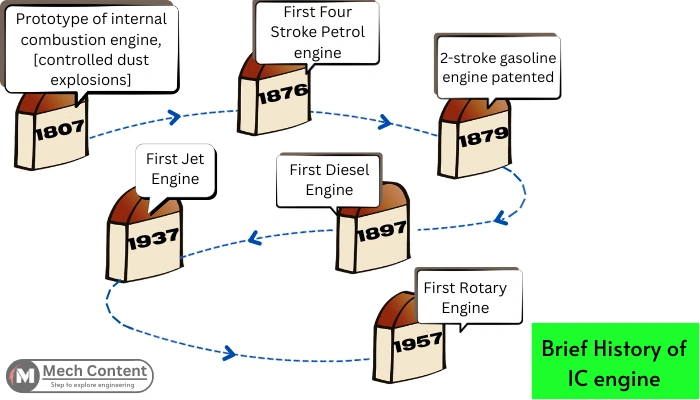
Types of Internal combustion engines:
There is a wide range of IC engines that are being used to serve different purposes in various applications. Mostly the IC engines are classified on different basis as follows:
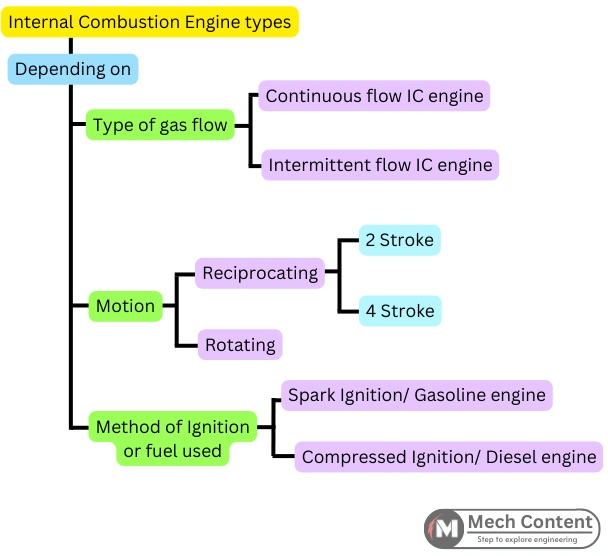
1] Type of gas flow:
Based on type of gas flow, the IC engines are classified as,
a] Continuous flow IC engines:
In this engine, the flow of gases is continuous and they go through various thermodynamic processes simultaneously. Hence here, the combustion of fuel also takes place continuously.
E.g.: Gas turbine.
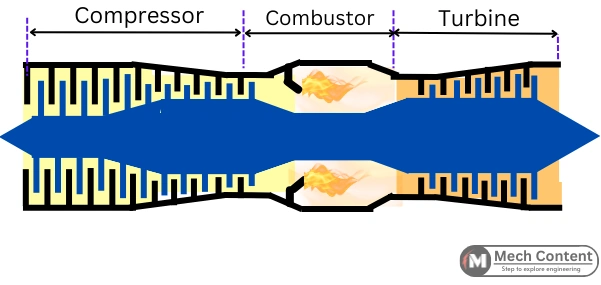
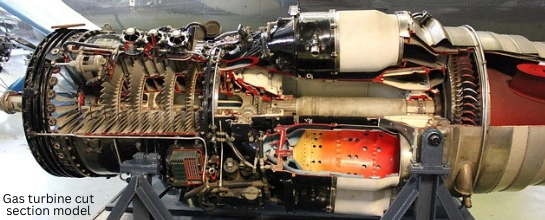
b] Intermittent flow IC engines:
In these engines, the flow of gases is not continuous. A certain volume of charge passes through the different processes [Suction-Compression-Combustion-Exhaust].
All these processes together constitute a single combustion cycle. Hence in these engines, combustion takes place periodically not continuously.
E.g.: Reciprocating engines
2] Type of motion:
Based on the motion of components, the IC engines are classified as,
a] Reciprocating engines:
These engine uses reciprocating component (piston) to convert pressure energy into mechanical work.
The piston reciprocates to continuously change the volume of the combustion chamber, which helps to carry out different processes in the engine.
b] Rotary engines:
Rotary engines perform the same processes as reciprocating engines. But here all the processes are carried out with the help of an eccentrically rotating rotor.
The below shown Wankel engine is an example of a rotary engine.
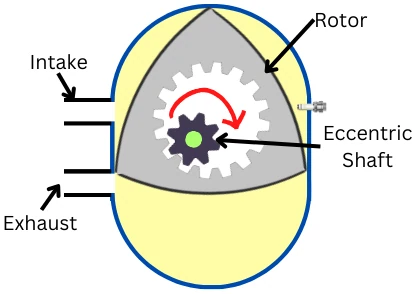
It has an oval-shaped casing and a triangular-shaped rotor. Each side of the triangular rotor has a convex shape.
While rotating, the three edges of the rotor continuously touch the casing inner surface. Thus, it creates three separate moving working chambers for completing the combustion process. The volume of these working chambers changes continuously during rotation.
The four processes of the combustion cycle (Suction-Compression-Ignition-Exhaust) are carried out at the four different portions of the casing.
3] Number of strokes:
Based on the number of strokes of piston required to complete a single combustion cycle, IC engines are classified as,
a] Two-stroke engine:
In two-stroke engines, all processes are completed within two strokes of the piston or within 1 revolution of the crankshaft.
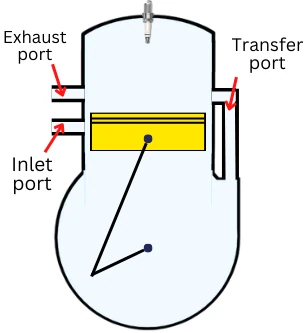
For this engine, the power stroke occurs during each revolution of the crankshaft. Therefore, it produces more power in comparison with same size four-stroke engine.
b] Four-stroke engine:
For four-stroke engines, a single combustion cycle consists of four strokes of the piston, i.e. two revolutions of the crankshaft. Within four strokes, the engine performs four different processes i.e. Suction-Compression-Combustion-Exhaust.
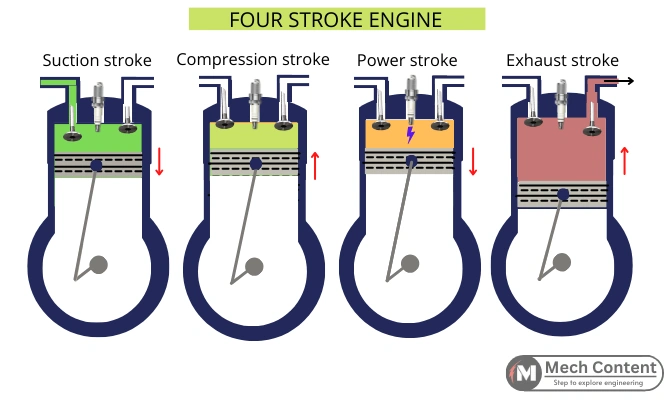
In 4-stroke engines, the flow of gases in the engine is controlled by valves with the help of camshaft.
4] Ignition:
Depending on the method of starting the combustion process, the engines are classified as,
a] Spark-ignition (Petrol) engine:
In these engines, the combustion of the air-fuel mixture starts with the generation of a spark. For this purpose, it uses a spark plug at the top of the combustion chamber. The high voltage across the electrodes of the spark plug generates the spark into the compressed charge.
As these engines use spark plug for ignition, it requires a comparatively lower compression ratio.
b] Compression ignition (CI) engine:
In the CI engine, the fuel get self-ignited due to the heat of compression gained by air during compression stroke. In this engine, only air is sucked into the cylinder during suction stroke and then compressed with a high compression ratio.
To attain a higher temperature of the air at the end of the compression stroke, these engines have a higher compression ratio (14 to 25) than the SI engines.
The engine uses a fuel injector at the top of the combustion chamber.
At the end of compression, fuel is spread into the hot compressed air. As the temperature of air is above the self-ignition temperature of the fuel, it helps fuel to undergo self-ignition.
Major components of reciprocating IC engine:
The reciprocating engine is a highly utilized type of internal combustion (IC) engine, with applications spanning various sectors. Below are some of the key components of this engine.
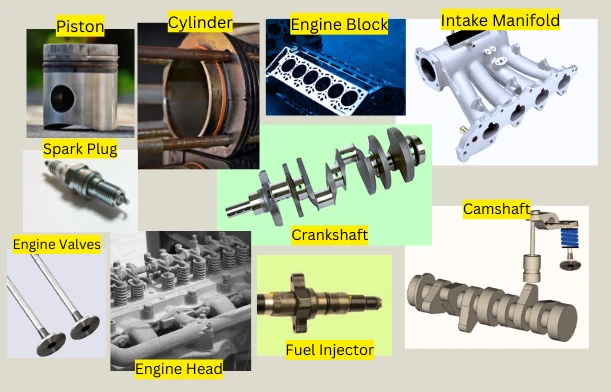
1] Piston:
Piston is the critical component in the engine that reciprocates between TDC (Top dead center) and BDC (Bottom dead center) inside the cylinder to perform different processes.
The piston is connected to the connecting rod with the help of a gudgeon pin.
Key Functions:
- Sealing the combustion gases: There are piston rings mounted on the piston which helps in sealing the combustion gases.
- Sucks fresh Charge: During the suction stroke, the piston helps to take fresh charge inside of the chamber.
- Fresh charge compression: During compression stroke helps to compress the charge.
- Expels out Burnt Gases: During the exhaust stroke helps to remove the burnt gases from the chamber through an engine exhaust valve.
- Heat Transfer: Transfers heat from piston to cylinder.
2] Cylinder: It is a cylindrical chamber in which the piston moves. The exchange of fresh or exhaust gases occurs inside the cylinder.
Features:
- Guides the piston to reciprocate.
- Enclosure for combustion: All the combustion processes are carried inside the cylinder.
3] Cylinder head:
The cylinder head fits above the engine cylinder forming the top enclosure for creating combustion chamber.
It houses many engine components: The inlet valve, exhaust valve, fuel injector/spark plug are mounted on the cylinder head.
4] Inlet Valves: Controls the entry of fresh charge to engine.
Location: The inlet valve is located at the engine intake port, from where the fresh charge enters inside the cylinder.
Characteristics:
- The inlet valve is open and closed by the rotation of the camshaft.
- The Inlet valve is in the open position during the suction stroke and remains closed during other strokes.
5] Exhaust valve: Controls the exit of exhaust gases from the engine
Location: The exhaust valve is located at the engine exhaust port, from where the exhaust gases are released to the exhaust manifold.
Characteristics:
- The opening and closing of the exhaust valve is also done by the rotation of the camshaft.
- The exhaust valve is in the open position during the exhaust stroke and remains closed during the other strokes.
6] Spark plug:
The petrol engines have spark plug to initiate combustion of air-fuel mixture, by generating electric spark.
The precise timing of spark generation is crucial for achieving complete combustion of the charge, maximizing power output, and increasing efficiency.
7] Fuel injector:
The fuel injector is an essential component of a diesel engine. It is responsible for delivering atomized fuel into the hot compressed air at the end of the compression stroke.
It operates under high pressure due to the high-pressure fuel supplied by the fuel injection pumps.
8] Crankshaft: The crankshaft is the engine’s first rotating component.
Features:
- It converts the oscillatory motion of the connecting rod into rotary motion.
- The crankshaft connects to the connecting rod via the crankpin and is further connected to the engine flywheel.
- Rotates the camshaft through engine timing mechanism.
9] Camshaft:
In four stroke engines, the camshaft is responsible for actuating the valves at the correct time. It consists of a shaft with cam lobes that open and close the valves for the precise interval.
The camshaft is powered by the crankshaft through timing mechanism and rotates at half the speed of the crankshaft.
10] Engine block:
The engine block, also known as the cylinder block, houses the engine’s cylinders and has passages for coolant and oil.
It’s a crucial part of the engine where various components connect, such as pistons, cylinder head, cylinder liners, crankshaft, crankcase, etc. It is built to handle high temperatures and pressures.
11] Fuel injection system:
Fuel injection systems offer excellent control over the air-fuel ratio.
In modern SI engines, using a fuel injection system instead of a carburetor provides greater flexibility and accuracy in adjusting the air-fuel ratio. These systems can continuously adjust the fuel supply to the cylinders, to optimize performance.
The different fuel injection systems in SI engines include single-point fuel injection, multi-point fuel injection, direct injection, and sequential fuel injection.
Fuel injection systems in diesel engines include indirect injection, direct injection, and common rail direct injection.
12] Crankcase:
The crankcase is a housing used to mount and enclose the camshaft.
Functions:
- Provides support for the crankshaft.
- Encloses vital components such as the crankshaft and bearings.
- Acts as an oil sump in four-stroke engines.
- Assists in the cooling of lubricating oil.
13] Intake Manifold:
Intake or inlet manifold supplies fresh charge to the engine cylinders. In multi cylinder engine, it ensures the even distribution of charge to all cylinders.
Functions:
- Distribution of charge to cylinders
- Provides a mounting point for fuel injectors and sensors
- Serves as vacuum source for various engine functions
How does an Internal combustion (IC) engine work?
The working of an internal combustion engine consists of the following common processes.
Suction, Compression, Combustion (and Expansion) and Exhaust
In intermittent flow engines, these processes are carried periodically in the form of repetitive cycles while in Continuous flow IC engines all processes are carried simultaneously in different portions of the engine.
See below figure-A for an intermittent flow IC engine in which the processes repeat periodically for each intake charge.
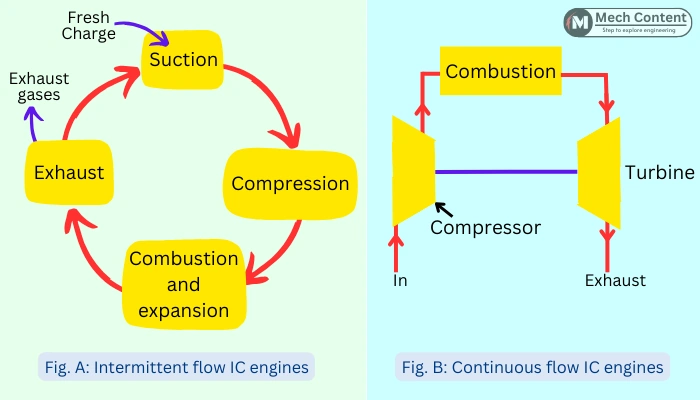
See another figure-B for Continuous flow IC engines in which all processes occur simultaneously.
Let’s look at each process in IC engines in brief.
1] Suction: During this process, an amount of fresh air or air-fuel mixture enters the engine.
2] Compression: The intake charge is compressed to increase the pressure and temperature. In a reciprocating engine, compression is done by the reciprocating piston.
In continuous flow engines, it is done by the axial compressor consisting of stator and rotor blades.
3] Combustion and Expansion: In this process, the compressed charge is ignited to generate high-pressure combustion products. In SI engines, the ignition process starts with the generation of a spark while in CI engines fuel is injected into the compressed air which leads to self-ignition.
These high-pressure combustion products are used for performing mechanical work. In piston-cylinder engines, the high-pressure gases expand with pushing the piston that further rotates the crank and crankshaft.
In gas turbine power plants, the exhaust gases are used to rotate the turbine blades. The gas turbine and other continuous flow IC engines used in aircraft use these exhaust gases to provide thrust to propel the aircraft.
4] Exhaust: The low-pressure gases are ejected to the atmosphere.
Internal combustion engine efficiency:
Heading is about efficiency, so first connect it with losses, then start.
The efficiencies of the IC engine depend on the different engine losses.
The below figure shows the losses that occur in the IC engine while converting the chemical energy of the fuel into mechanical energy.
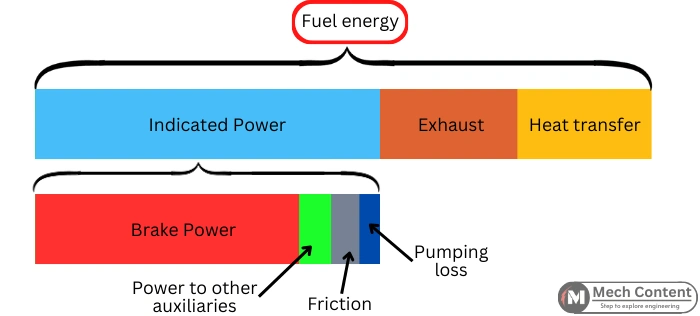
The different types of efficiencies to measure the performance of an IC engine are as follows.
1] Indicated thermal efficiency: Indicated thermal efficiency defines the ratio of indicated power to the rate of heat energy of the fuel. Here indicated power means the power generated inside the cylinder by the fuel combustion.
2] Brake thermal efficiency: Brake thermal efficiency indicates how efficiently fuel energy gets converted into brake power, i.e., Power at the crankshaft. It is calculated by taking the ratio of brake power to the rate of heat energy of the fuel.
3] Volumetric efficiency: Volumetric efficiency of IC engine is the ratio of the volume of charge sucked during the suction stroke to the swept volume.
4] Mechanical efficiency: It indicates how efficiently indicated power gets converted into the brake power. It is given by taking the ratio of Brake power to the Indicated power.
5] Relative efficiency: It is the ratio of indicated thermal efficiency and the air standard efficiency of the reversible cycle.
6] Air standard efficiency: It is the ideal efficiency calculated by considering air as a working medium. It is also known as the efficiency of an Air standard cycle.
Uses of IC engines:
The IC engines are a power source for many machines. It is used for the following different purposes:
1] Propel Road and water vehicles: The IC engines are the main power source of the vehicles used for transportation. The IC engines are used to generate power ranging from 2.5 KW for propeling a road moped to 80 MW for propeling cruise ships.
2] Create thrust in Aircraft: The IC engines used in aircraft generate a high amount of thrust, that helps it to fly faster.
3] Power generation: The IC engines are also used to rotate the electrical generators for power generation. Gas turbines and diesel generators are kinds of IC engines used for electrical power generation.
4] To power equipment: IC engines are also used to run different equipment like Lawn mowers, Chain-saws, Concrete mixers, Water pumps, etc.
You may like to read: