A Lorry crawling with tons of load, Tractor pulling a plow are some of the examples that say how powerful four-stroke diesel engines are. These are the commonly used IC engines that power various heavy-duty applications like trucks, buses, farm and construction machinery, power generators, etc.
This article focuses on the principal, construction, working, and other details of the four-stroke diesel engine. Let’s begin.
In this article, we’re going to discuss:
- What is Four stroke diesel engine?
- Working principle:
- Parts and function:
- Working of four stroke diesel engine:
- Valve timing diagram:
- Advantages of four stroke diesel engine:
- Disadvantages of four stroke diesel engine:
- Applications of four stroke diesel engine:
What is Four stroke diesel engine?
Four-stroke diesel engines are internal combustion engines that run on the principle of the diesel cycle and complete a single cycle within four strokes of the piston.
The engine was invented by the German engineer Rudolf diesel, hence the engine and the fuel used for it are recognized by the name Diesel.
In four-stroke diesel engines, the combustion of the fuel occurs due to the rise in temperature of the intake air (above the self-ignition temperature of fuel) due to the higher compression. Therefore because of the method of ignition, these engines are also known as compression ignition (CI) engines.
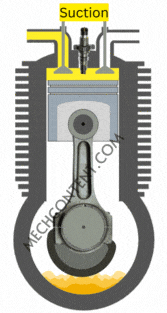
These engines have a comparatively higher compression ratio than gasoline (petrol) engines ranging from 14:1 to 25:1 (Which means that it compresses the air up to 1/14th to 1/25th of the initial volume).
The higher compression ratio in the diesel engine helps to achieve higher peak pressure during the combustion, as well as the longer stroke length helps to obtain more torque during the expansion stroke. As it generates high torque, it is more suitable for running heavy equipment.
In this engine, the fuel is mixed into the compressed air with the help of a fuel injector. The high-pressure fuel injection assists in the better atomization of fuel and the higher temperature helps for the self-ignition of the fuel.
Due to the higher compression ratio, these engines have more robust construction, hence it runs longer before the major overhaul.
Mostly four-stroke diesel engines are considered the most fuel-efficient engines among practical internal combustion engines as it has higher thermal efficiency.
These engines don’t require throttling device to control the intake of air. It takes the same amount of air intake during each suction stroke. While the speed and torque are controlled by changing the air-fuel ratio by controlling the intake of fuel.
Thus, the accelerator pedal is used to control the intake of diesel instead of the intake of air.
Working principle:
The four-stroke diesel engine works on the principle of the thermodynamic diesel cycle. The below figure shows the ideal diesel cycle on P-V and T-S plots.
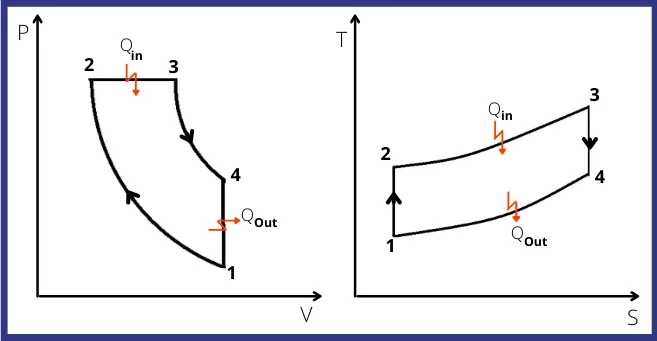
The ideal Diesel cycle consists of the following four processes:
- Process 1-2: Isentropic compression
- Process 2-3: Constant pressure heat addition
- Process 3-4: Isentropic expansion
- Process 4-1: Constant volume heat rejection
Parts and function:
These engines have a more durable construction that can withstand pressure and temperature peaks. The basic four-stroke diesel engine consists of the following components.
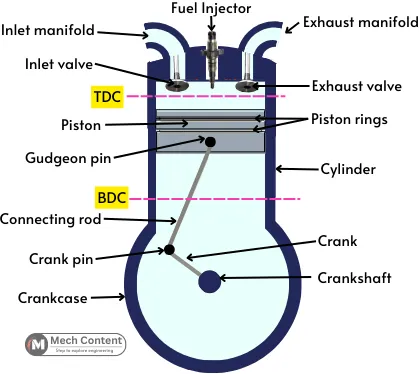
1] Cylinder block: The cylinder block (Engine block) is the largest component of the diesel engine. It has bores that act as a cylinder for the movement of the piston.
The diesel engines have thicker cylinder heads to bear higher stress resulting due to a higher compression ratio.
2] Cylinder head: The cylinder head is mounted on the top of the cylinder block and also forms the top region of the combustion chamber. The cylinder head of the diesel engine is different than the gasoline engine because of the presence of a fuel injector.
3] Fuel injector: In this engine, the fuel injector is the vital component that makes it different from gasoline engines. The fuel injector is used to inject and atomize the metered amount of fuel into the compressed air.
For better atomization, the fuel is injected at higher pressure with the help of a fuel injection pump.
4] Piston: The piston in the diesel engine is different as it has a piston bowl for the effective mixing of injected fuel with the air. In this engine, the piston has to travel a longer stroke length because of the higher compression ratio.
5] Connecting rod: Connecting rod connects the reciprocating piston to the rotating crankshaft. Its small end is connected to the piston using a gudgeon pin and the big end is mounted on the crankpin journal of the crankshaft.
6] Crankshaft: The crankshaft is the rotating component that draws power from the oscillating connecting rod. From the crankshaft, the power is transferred to the transmission unit.
7] Valves and valve mechanism: The intake valve controls the flow of air entering the cylinder while the exhaust valve controls the flow of the exhaust gases leaving the cylinder. These valves are run by the crankshaft with the help of a valve timing mechanism.
Other than the above components, the cooling system, lubricating system, fuel injection system, etc. also perform a vital role in the performance of these engines.
Working of four stroke diesel engine:
The working of the four-stroke diesel engine is nearly similar to the four-stroke petrol engine (Suck, Squeeze, Bang, Blow) except the method of combustion.
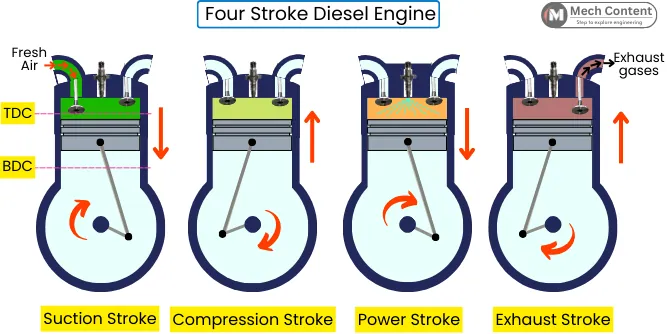
Each power cycle of the four-stroke diesel engine consists of the following four strokes.
1] Suction:
At the start of the suction stroke, the piston is at the top dead center (TDC) with the intake valve in an open situation and the exhaust valve in a closed situation.
During the suction stroke when the piston moves from TDC to BDC, the piston creates a partial vacuum inside the cylinder. Thus due to the pressure difference between the intake manifold and the cylinder, the air is pulled into the cylinder through the intake port.
At the end of the suction stroke, the intake valve becomes closed.
2] Compression:
During the compression stroke, the air trapped inside the cylinder is compressed at higher pressure to raise the temperature of the air.
During this stroke, both the valves remain in a closed situation and the piston travels from the BDC to the TDC.
The higher compression ratio of the diesel engine helps to raise the temperature of the air above the self-ignition temperature of the fuel.
3] Expansion or power stroke:
Just before the piston reaches TDC, the fuel injector starts the injection of the fuel into the hot compressed air. Due to the higher temperature, the atomized fuel undergoes self-ignition and starts the combustion. The combustion of the fuel ends when the fuel injector stops injecting the fuel.
This develops high-pressure gases (Combustion products) inside a combustion chamber that exerts pressure on the piston surface. Thus the piston is pushed toward BDC, to allow the combustion products to expand.
During this stroke, as the piston draws power from the expansion of the high-pressure gases, this stroke is also known as a power stroke.
During this stroke, the intake and exhaust valve remains in the closed situation.
4] Exhaust:
At the end of the expansion stroke, just before the piston reaches BDC, the exhaust valve becomes open.
As soon as the valve opens, the exhaust gases inside the cylinder start to enter into the exhaust manifold. Due to the piston travels from the BDC to TDC, the exhaust gases are pushed outside of the cylinder.
At the end of the exhaust stroke, the exhaust valve becomes closed and the engine becomes ready for the suction stroke of the next cycle.
Hence In this way cycle continues to obtain power from the 4-stroke diesel engine.
Valve timing diagram:
The valve timing diagram represents the instances of opening and closing of the valves with respect to the crank position. The below figure is the actual valve timing diagram for the four-stroke diesel engine that show the instance of valve openings and spill time of the fuel injector.
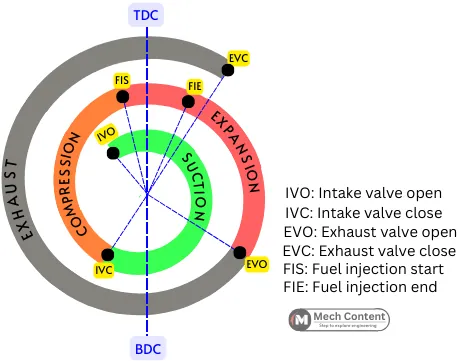
As shown in the above figure, the engine cycle starts with the opening of the intake valve and ends with the closing of the exhaust valve.
As shown above, the intake valve opens a few degrees before the TDC. It causes effective scavenging of the cylinder due to the overlapping of the intake and exhaust valves.
The intake valve closes a few degrees after the piston leaves BDC. It ensures maximum air enters the combustion chamber due to the inertia of the flow of the air coming from the intake manifold.
As shown above, the fuel injection starts a few degrees before the piston reaches TDC. The combustion of the fuel does not start exactly during the start of the fuel injection.
There is a duration between the start of fuel injection and the start of combustion (Ignition delay). The early injection of fuel ensures that the combustion starts when the piston reaches TDC.
The exhaust valve opens a few degrees before the piston reaches BDC. It helps to lower the pressure inside the cylinder when the piston reaches BDC. Thus during the exhaust stroke, the piston can easily move in an upward direction.
The exhaust valve closes a few degrees after the piston leaves the TDC, it causes overlapping of the valves for effective scavenging.
Advantages of four stroke diesel engine:
The four-stroke diesel engine has the following advantages:
- Higher torque generation: Due to the higher compression ratio, the diesel engine generates higher torque.
- High power generation: The higher torque leads to high power generation.
- The carburetor is not necessary for the mixing of air and fuel.
- It has a lower running cost.
- Lower fuel cost in comparison with gasoline or petrol engine.
- The spark plug is not necessary for ignition.
- These engines have higher thermal efficiency in comparison with petrol engines.
- Suitable for heavy load applications.
- It generates higher torque at a lower speed.
- Less fuel consumption as diesel is a denser fluid.
Disadvantages of four stroke diesel engine:
The four-stroke diesel engine has the following disadvantages:
- It requires a high-pressure fuel injection system.
- The engine works at a higher compression ratio.
- The maintenance cost is higher in comparison with gasoline engines.
- Most diesel engines are noisy in operation.
- Four-stroke diesel engines are bulkier than petrol engines.
- During the winter season, it becomes difficult to start the engine.
- It creates more vibrations.
- The heater is necessary during the cold season to start the engine.
Applications of four stroke diesel engine:
The four-stroke diesel engine is used in different automobiles and other applications such as follows:
- Train
- Boat and ships
- Truck
- Wagon
- Tractor and other farming machines
- Earthmovers
- Cars
- Diesel generators
FAQ’s:
-
What is Four stroke diesel engine?
The Four stroke diesel engine is the internal combustion engine that works on thermodynamic diesel cycle in which one power cycle consists of four consecutive strokes which are suction, compression, power and exhaust.
-
How does a Four stroke diesel engine Work?
The four stroke diesel engine works on principle of diesel cycle in which the fuel is ignite by increasing the temperature of the air above the self-ignition temperature of fuel.
You may like to read: